By William Pearce
Around 1936, the RLM (Reichsluftfahrtministerium, or Germany Air Ministry) sought the design of an 1,800 hp (1,342 kW) engine for the next generation of bomber aircraft. Otto Mader, the head of the Junkers Flugzeug- und Motorenwerke AG (Junkers Aircraft and Motor Works) research institute in Dessau, considered various V and H configurations for such an engine. However, each configuration had various drawbacks. Mader discussed the engine requirements with Ferdinand Brandner and tasked him with the project. Brandner was an experienced engine and railway engineer that had recently joined Junkers.

A Junkers Jumo 222 A/B-1 engine with a short gear reduction housing. First run in 1939, the Jumo 222 represented what was believed to be the next generation of German aircraft engines. Note the coolant pump below the gear reduction housing and the fuel injection pump between the intake manifolds.
Brandner and his team set a goal of 2,000 hp (1,491 kW) and immediately began designing a completely new engine. The engine originally carried the manufacturer’s designation P2001, and Junkers submitted a proposal that outlined the 1,900 hp (1,417 kW) engine to the RLM on 4 December 1936. On 4 May 1937, the RLM placed an order for a prototype P2001 engine, which would officially become the Junkers Jumo 222 on 4 April 1938. Brandner and his team continued to work on the engine design, which was finalized on 4 June 1937. Nearly from the start, the Jumo 222 was intended to power the improved development of the Junkers Ju 88 bomber, which originally carrier the manufacturer’s designation EF 73 (Entwicklungs-Flugzeug 73, Development Aircraft 73). Later, the aircraft would become the Ju 288 bomber.
The Junkers Jumo 222 was a liquid-cooled inline radial. The engine had six cylinder banks placed radially around the crankcase at 60 degree angles, with the left and right banks horizontal. Each of the six cylinder banks had four cylinders, giving the engine a total of 24 cylinders. The outer points of the six cylinder banks formed a hexagon, making the Jumo 222 one of the rare hexagonal engines, like the Curtiss H-1640 Chieftain, the Wright H-2120, the SNCM 137, and the Dobrynin series of aircraft engines.
The two-piece aluminum crankcase was split horizontally below the left and right cylinder banks. The top four cylinder banks were on the upper crankcase half, and the bottom two cylinder banks were on the lower crankcase half. The two crankcase halves were joined by 11 studs on each side and four long studs that extended from the center main bearing. The one-piece balanced crankshaft was supported in the upper crankcase half by five plain main bearings. Each main bearing cap was secured by four vertical studs and one very long stud that passed transversely through the entire crankcase. Mounted on each of the crankshaft’s four throws was a rather typical radial-engine master rod with five articulating rods. The connecting rod was split, with three articulating rods attached to the bottom and the master rod flanked by two articulated rods on the top. The two pieces of the connecting rod were joined by four bolts. Reportedly, the master connecting rods for cylinder rows 1 and 4 (front and rear) were located in bank 5 (7 o’clock position), and cylinder rows 2 and 3 (middle two) were located in bank 6 (5 o’clock position). However, a drawing of the Jumo 222 depicts a master rod in one of the upper cylinder banks. It appears the drawing shows the configuration used in early engines, and the master rods were relocated to the lower cylinder banks in later variants. The flat-top aluminum pistons were rather short with two compression rings and two oil rings, all located above the piston pin. The engine’s compression ratio was 6.5 to 1.

Rear view of the Jumo 222 A/B-1 illustrating the supercharger and its two-sided inlet. Note how the intake manifold branches to serve two adjacent cylinder banks. The engine’s magnetos are mounted to the upper cylinder banks, and the oil pump is mounted under the supercharger.
The steel cylinder barrels were installed through the crankcase and sealed at their lower end by three rubber rings. Near the bottom of each barrel was a flange with four long studs that extended up through the cylinder head. The tightening of these studs drew the barrel up into the cylinder head and sealed it with a tapered aluminum ring to the combustion chamber. The combustion chamber was wedge-shaped with the exhaust valve on the short side. The cylinder head of each bank was a single aluminum casting secured to the crankcase by 10 studs. At the top of each cylinder were two intake valves and one sodium-cooled exhaust valve. A fuel injector was positioned between the two intake valves, and a spark plug was positioned between each of the two intake valves and the common exhaust valve. The valves for each cylinder bank were actuated via rockers by a single overhead camshaft. The rear of each camshaft was driven from the crankshaft by a series of spur gears. The camshafts turned clockwise for cylinder banks 1, 3, and 5 and counterclockwise for cylinder banks 2, 4, and 6.
Attached to the front of the crankcase was a planetary gear reduction with the propeller shaft positioned at the center of the engine. While the crankshaft turned clockwise, different gear reduction housings could be used to turn the propeller in either direction. The propeller of the Jumo 222 A, C, E and G models turned counterclockwise at .368 crankshaft speed. The counterclockwise gear reduction used a fixed planetary carrier with the propeller shaft driven from the free outer ring gear. The propeller of the Jumo 222 B, D, F and H models turned clockwise at .364 crankshaft speed. The propeller shaft of the clockwise gear reduction was driven from the free planetary carrier that rotated against the fixed outer ring gear. The clockwise gear reduction on the Jumo 222 B, D, F and H models weighed approximately 66 lb (30 kg) additional. A short gear reduction housing was available, but the extended version was most common. An inertia starter was mounted to the crankcase above the gear reduction housing, and the coolant pump was mounted below the gear reduction housing.
Attached to the rear of the crankcase was an accessory housing followed by the single-stage, two-speed supercharger. The supercharger impeller was 12.8 in (325 mm) in diameter and turned at 6.70 and 9.16 times crankshaft speed in low and high gears. It provided 8.8 lb (.61 bar) of boost for takeoff. Each of the three outlets from the supercharger fed an intake pipe that branched into two manifolds. These manifolds were positioned between the cylinder Vees at the 4, 8, and 12 o’clock positions, and each fed once cylinder bank. An eight-cylinder fuel injection pump was also positioned between the intake manifolds in each of these cylinder Vees. Individual exhaust stacks were fitted to the cylinder heads between the bank Vees at the 2, 6, and 10 o’clock positions. Engine mounting pads were located on the crankcase between the bank Vees at the 2 and 10 o’clock positions.

Sectional view of the Jumo 222 with a master connecting rod in an upper cylinder bank. This is most likely a Jumo 222 A/B-1 engine, as it appears to have an early H-beam articulated connecting rod design. Later variants had the master connecting rods in the lower banks and I-bean articulated connecting rods. Note the wedge-shaped combustion chambers.
When viewed from the rear, the cylinder banks were numbered counterclockwise starting at the right horizontal bank at the 3 o’clock position, which was bank 1. Bank 2 was at 1 o’clock, bank 3 was at 11 o’clock, and so on. The front cylinder of each bank was No 1, and the rear cylinder was No 4. Each of the upper two cylinder banks had a magneto mounted to its rear. Each magneto fired all the cylinders for three banks with no redundancy. If a magneto failed, one entire side of the engine would not fire. Cylinders in opposite banks fired simultaneously. The firing order changed during the engine’s development. The following firing order is specific to the Jumo 222 E/F but may be applicable to other engine models. The Jumo 222 E/F’s firing order was as follows: Bank 2 Cylinder 1 & Bank 5 Cylinder 2, B1C1 & B4C2, B6C4 & B3C3, B2C3 & B5C4, B1C2 & B4C1, B6C2 & B3C1, B2C4 & B5C3, B1C4 & B4C3, B6C1 & B3C2, B2C2 & B5C1, B1C3 & B4C4, and B6C3 & B3C4.
The Junkers Jumo 222 A/B-1 had a 5.31 in (135 mm) bore and stroke. The engine had a total displacement of 2,830 cu in (46.38 L). The Jumo 222 A/B-1 initially produced 2,000 hp (1,491 kW) at 3,200 rpm. At the expense of reliability, further development eventually pushed its maximum power at 3,200 rpm to 2,500 hp (1,417 kW) for takeoff and 2,200 hp (1,641 kW) at 16,404 ft (5,000 m). Climbing power at 2,900 rpm was 2,260 hp (1,685 kW) at sea level and 2,090 hp (1,559 kW) at 16,404 ft. Cruising power at 2,700 rpm was 1,900 hp (1,617 kW) at sea level and 1,700 hp (1,268 kW) at 17,060 ft (5,200 m). The engine’s fuel consumption at cruise power was .477 lb/hp/hr (290 g/kW/h) at sea level. The Jumo 222 A-1 weighed 2,690 lb (1,220 kg), and the Jumo 222 B-1 weighed 2,745 lb (1,245 kg). The engine had a diameter of 3 ft 10 in (1.16 m) and was 7 ft 5 in (2.25 m) long.
In early 1938, RLM requested that the Jumo 222’s output be increased to 2,000 hp (1,491 kW). Since the engine was designed from the start for 2,000 hp (1,491 kW), this request did not present any issues, but it foreshadowed what was to come. A single-cylinder test engine was first run in March 1938, followed by one complete row of six cylinders in June 1938. On 24 April 1939, a complete Jumo 222 A/B-1 was run for the first time and taken up to 3,000 rpm. The engine was disassembled and inspected after the test and showed no signs of wear or issues.
In May 1939, Junkers submitted to the RLM design proposals for the Jumo 222-powered EF 73 (Ju 88 development) bomber aircraft. Incidentally, EF 74 was the same basic aircraft but powered by Jumo 224 engines. Encouraged by Junkers’ proposal, the RLM issued specifications in July 1939 for a new medium bomber capable of high-speeds. Originally known as Kampfflugzeug B (Warplane B), the aircraft proposal was eventually renamed Bomber B. The Bomber B specification requested an aircraft that could carry a 2,000 kg (4,410 lb) bomb load 3,600 km (2,237 mi) and have a top speed of 600 km/h (373 mph). For alternatives to the Jumo 222, the RLM requested engine designs from BMW and Daimler-Benz. The Junkers Bomber B proposal became the Ju 288, and other entrants included the Arado E.240, Focke-Wulf Fw 191, Dornier Do 317, and later, Henschel Hs 130C. The additional engine proposals were the BMW 802 18-cylinder radial and the Daimler-Benz DB 604 X-24.

A Jumo 222 installed in the nose of a Junkers Ju 52 transport test bed. The engine was equipped with exhaust manifolds to duct the fumes away from the cockpit. Note how the Jumo 222’s engine nacelle appears no larger than those for the Ju 52’s standard 725 hp (541 kW) engines.
The Ju 288 was selected for production, although prototypes of the Fw 191, Do 317, and Hs 130C would also be built. The Ju 288 and the Fw 191 were to be powered by the Jumo 222, which was ultimately selected over the other engines. The Jumo 222 was also planned for a future development of the Do 317. When war officially broke out on 1 September 1939, the Ju 288 was perceived as an aircraft needed for a decisive victory. It and the 2,000 hp (1,491 kW) Jumo 222 A/B-1 were given a high priority. At the time, three complete Jumo 222 A/B-1 engines were running on test stands. During 1939, Junkers had formed the Otto-Mader-Werke at Dessau to focus on engine design and development. This division was run by Mader and worked on the Jumo 222 and Jumo 004 (turbojet) engines.
In March 1940, the Jumo 222 A/B-1 achieved 2,000 hp (1,491 kW) for the first time, but some difficulties were encountered at this higher output with inadequate lubrication and connecting rod issues. Modifications were made to resolve the deficiencies, and the revised engine was running in August 1940. For flight testing, the Jumo 222 was installed in the center position of a Junkers Ju 52 trimotor transport and made its first flight on 3 November 1940. However, the Jumo 222 was not ready to be installed in the Ju 288, and the aircraft made its first flight on 29 November 1940 powered by 14-cylinder BMW 801 radial engines.
In April 1941, the Jumo 222 A/B-1 completed a 100-hour type test at 2,000 hp (1,491 kW), running at 2,860 rpm. Some of the issues during the test included spark plug damage after 60 hours, a leaking injection pump controller at 75 hours, and a camshaft bearing block failure after 88 hours. When the engine was dismantled after the test, coolant and fuel leaks were discovered, but they were not considered serious. Based on the overall positive results of the 100-hour test, the RLM ordered the Jumo 222 into production on 30 April 1941. The engine would be built at the new Flugmotorenwerke Ostmark (Aircraft Engine Factory in annexed Austria) plant under construction in Wiener Neudorf, Austria, with production expected to start on 30 August 1942. A monthly output of 1,000 engines was forecasted.
Starting in mid-1940, the RLM began to alter requirements for the Ju 288. A fourth crew member, additional equipment, and airframe changes resulted in the aircraft’s weight increasing to the point that 2,000 hp (1,491 kW) was no longer sufficient for the Ju 288 to achieve its originally-specified performance. Around mid-1941, the RLM requested that the Jumo 222 produce 2,500 hp (1,864 kW) for the Ju 288. Junkers had foreseen this request and began developing the Jumo 222 A/B-2 in 1940 to reliably produce 2,500 hp (1,864 kW) and resolve issues encountered with the early engines.

A 2,000 hp (1,491 kW) Jumo 222 A/B-1 installed in a Junkers Ju 288 engine nacelle. Note the individual exhaust stacks protruding from the cowling.
The Jumo 222 A/B-2’s cylinder bore was increased .20 in (5 mm) to 5.51 in (140 mm), while its stroke remained unchanged at 5.31 in (135 mm). This change increased the Jumo 222 A/B-2’s displacement by 214 cu in (3.50 L) to 3,044 cu in (49.88 L). The H-beam articulated connecting rods of the early engines were replaced with an I-bean articulated connecting rod design. The engine’s compression ratio may have been raised to 6.735 to 1, and valve diameters may have been altered slightly. The Jumo 222 A/B-2 had a balance pipe between the intake manifolds of adjacent cylinder banks. Engine speed was limited to 2,900 rpm in an attempt to increase its reliability. The Jumo 222 A/B-2’s maximum power at 2,900 rpm was 2,500 hp (1,864 kW) for takeoff and 2,490 hp (1,857 kW) at 16,404 ft (5,000 m). Climbing power at 2,700 rpm was 2,250 hp (1,678 kW) at sea level and 2,050 hp (1,529 kW) at 16,404 ft (5,000 m). Cruising power at 2,500 rpm was 1,900 hp (1,417 kW) at sea level and 1,750 hp (1,305 kW) at 16,404 ft (5,000 m). The engine’s fuel consumption at cruise power was .449 lb/hp/hr (273 g/KW/h) at sea level.
The Jumo 222 A/B-2 was first run in mid-1941 and was taken briefly to 3,000 hp (2,237 kW) by overboosting to 11.5 psi (.79 bar) in October 1941. However, the increased bore size created a harmonic resonance within the engine. With three Ju 52s serving as Jumo 222 test beds and a number of other engines on test stands, the entire project began to encounter significant issues. Connecting rod bearings were still a problem as was corrosion of the engine’s internal components. Despite the issues, the Jumo 222A/B-1-powered Ju 288 V5 made its maiden flight on 8 October 1941. Brandner had managed to talk his way onto the aircraft for the flight, which was completed without issue. For the Ju 288, the Jumo 222 turned a four-blade Junkers VS 7 propeller that was a 13 ft 1 in (4.0 m) in diameter. An annular radiator was positioned in the cowling, and experiments were conducted on Ju 288 V5 using a ducted spinner to deliver cooling air to the radiator.
As the manufacturing plant in Austria neared completion in late October 1941, it was clear that the Jumo 222 was not going to be ready for production. A decision was made to manufacture the Daimler-Benz DB 603 at the plant with production starting in March 1942. On 24 December 1941, the RLM cancelled the Jumo 222 for the Ju 288. The decision was based on the engine’s then-current takeoff rating of only 2,000 hp (1,491 kW), its ongoing issues, and its operational readiness not being sufficient for the Ju 288’s planned production schedule. The Ju 288 would be powered by DB 610 (two coupled DB 605s) engines, and Junkers would focus on developing the Jumo 213 inverted V-12. Work on the Jumo 222 would continue, but the engine was no longer a priority. Brandner stated that, at the time, various Jumo 222 engines had completed 20 100-hour test runs, and many at Junkers felt that the engine was basically ready for production. However, further issues with the connecting rod bearings caused a developmental delay that extended from January to March 1942.
The connecting rod bearing failures took a long time to resolve with experimentation of different bearing materials and lubrication techniques. Ultimately, a new connecting rod design was employed, the antimony alloy bearing material was replaced with a tin alloy, and the synthetic engine oil used was switched to a natural oil with an increased sulfur content. Due to tin shortages, antimony had been substituted early in the engine’s development.

A Jumo 222 A/B-2 or -3 engine with an extended gear reduction housing. Note the revised intake manifolds with a balance pipe joining the two at their center. Two engine mounting pads are visible between the upper cylinder banks.
the Jumo 222 A/B-3 was developed to cure the vibration and harmonic issues of the A/B-2 and with an improved supercharger to maintain power up to 20,997 ft (6,400 m). Along with a revised gear train, the engine incorporated all other revisions to improve reliability. The Jumo 222 A/B-3’s maximum power at 3,000 rpm was 2,500 hp (1,864 kW) for takeoff and 2,410 hp (1,797 kW) at 9,186 ft (2,800 m). Climbing power at 2,700 rpm was 2,250 hp (1,678 kW) at sea level and 1,980 hp (1,476 kW) at 20,997 ft (6,400 m). Cruising power at 2,500 rpm was 1,860 hp (1,387 kW) at sea level and 1,640 hp (1,223 kW) at 20,997 ft (6,400 m). The engine’s fuel consumption at cruise power was .463 lb/hp/hr (282 g/Kw/h) at sea level.
The Jumo 222 A/B-3 was developed quickly, and was first run in late 1941. Like the Jumo 222 A/B-2, it was briefly tested to 3,000 hp (2,237 kW) by overboosting to 11.5 psi (.79 bar) on 26 May 1942. The RLM became interested in the Jumo 222 A/B-3 and ordered it into production on 5 August 1942. Production would be undertaken at a plant in Prague in German-occupied Czechoslovakia. Optimistically, the first Jumo 222 A/B-3s were expected in October 1944 with a peak production of 1,500 engines per month achieved in September 1945. Running at 2,500 hp (1,864 kW), the Jumo 222 A/B-3 completed a 50-hour test on 9 December 1942 and a 100-hour test on 11 March 1943. The engine was tested in Ju 52s and Ju 288 aircraft, but the production plans were never realized.
The Fw 191 made its first flight in early 1942 and used BMW 801s. It was not until December 1942 that the Fw 191 V6 (third aircraft built) flew with Jumo 222 engines. With engine issues and constant changes to the underperforming bomber aircraft, the Bomber B program was cancelled in June 1943. Germany was short on resources, which were better utilized in the production of fighter aircraft rather than building troubled experimental bombers with problematic engines.
The Jumo 222 C/D was conceived in 1941 to produce 2,500–3,000 hp (1,864–2,237 kW) for high-altitude operations. The Jumo 222 C/D was designed and built with its bore increased to 5.71 in (145 mm) and its stroke increased to 5.51 in (140 mm). This gave the Jumo 222 C/D a total displacement of 3,386 cu in (55.48 L). The engine produced 3,000 hp (2,237 kW) at 3,000 rpm and could maintain much of that power up to 32,808 ft (10,000 m) thanks to an improved supercharger. Some reports indicate the Jumo 222 C/D was first run in mid-1942, but it was never given priority or considered for production until 1945, when a 3,000 hp (2,237 kW) engine was desperately needed. Apparently, two Jumo 222 C/D engines were completed, but the deteriorating war conditions shifted priorities and prevented them from being tested.

The Ju 288 V5 (A-series, three-man crew) was the first of the type to fly with Jumo 222 engines. The cowling incorporated an annular radiator that was fed via a ducted spinner. Subsequent prototypes powered by Jumo 222 engines used standard spinners.
In late 1943, the Jumo 222 E/F was developed from the A/B-3 series with a 5.51 in (140 mm) bore, 5.31 in (135 mm) stroke, and 3,044 cu in (49.88 L) displacement. The engine was equipped with a two-stage, two-speed supercharger. While the primary stage of the supercharger was mechanically driven, the auxiliary stage used an infinitely variable fluid coupling. An air-to-water aftercooler was incorporated on each of the three intake pipes between the supercharger and where the pipe branched into the two intake manifolds. Coolant for the aftercooler system was circulated by a separate pump. Reports indicate that the Jumo 222 E/F had sodium-cooled intake valves and a 6.75 to 1 compression ratio.
The Jumo 222 E/F’s maximum power at 3,000 rpm was 2,500 hp (1,864 kW) for takeoff and 1,930 hp (1,439 kW) at 29,528 ft (9,000 m). Climbing power at 2,700 rpm was 2,220 hp (1,655 kW) at sea level and 1,680 hp (1,253 kW) at 36,000 ft. Cruising power at 2,500 rpm was 1,840 hp (1,372 kW) at sea level and 1,400 hp (1,044 kW) at 34,689 ft (11,000 m). The engine’s fuel consumption at cruise power was .454 lb/hp/hr (276 g/kW/h) at sea level. At 42,651 ft (13,000 m), an output of 1,710 hp (1,275 kW) at 2,900 rpm was possible with GM 1 (Göring Mischung 1 / Göring Mixture 1) nitrous oxide injection. The addition of MW 50 (Methanol-Wasser 50), a 50-50 mixture of methanol and water injected into the induction system, further boosted performance by approximately 400 hp (298 kW) up to the engine’s critical altitude. The engine was 8 ft 2 in (2.50 m) long. The Jumo 222 E weighed 3,009 lb (1,365 kg), and the Jumo 222 F weighed 3,075 lb (1,395 kg). First run in 1944, the engine initially received a high priority. However, development and plans for mass production of the Jumo 222 E/F were halted in mid-1944 to focus resources on the Jägernotprogramm (Emergency Fighter Program).
Reports indicate that the Jumo 222 E/F was flown in Ju 288 V9, and presumably it was also tested in a Ju 52. Heinkel He 219 V16 was planned to test Jumo 222 A/B-3 engines, but Jumo E/F engines were used instead when the aircraft made its first flight on 23 July 1944. Estimates indicated that the Jumo E/F-powered He 219 would be capable of 414 mph (666 km/h) at 32,808 ft (10,000 m) and 435 mph (700 km/h) with MW 50 injection at 26,247 ft (8,000 m). With the shift in priorities, He 219 V16 made less than 20 flights, and the project was abandoned by January 1945. Six Jumo 222 E/F engines were finished by war’s end, and another four were partially completed.
In early 1944, the Jumo 222 G/H (sometimes referred to as the Jumo 222 Turbo) was developed from the A/B-3 series with a 5.51 in (140 mm) bore, 5.31 in (135 mm) stroke, and 3,044 cu in (49.88 L) displacement. The engine incorporated a turbocharger and intercoolers. Running at 3,200 rpm, the Jumo G/H produced 2,400 hp (1,790 kW) for takeoff and 2,070 hp (1,544 kW) at 40,354 ft (12,300 m). At 2,900 rpm, the engine produced 1,970 hp (1,469 kW) at 41,339 ft (12,600 m). A single Jumo 222 B-2 was used as the G/H test engine and made 22 runs before the end of the war, but it was not installed in any test aircraft.

The Ju 288 V9 (B-series, four-man crew) with standard spinners in flight. Just visible is the annular radiator mounted inside the cowling. Note the lower rows of exhaust stacks under the cowling.
On 28 April 1944, the Otto-Mader-Werke at Dessau, which was developing the Jumo aircraft engines, was heavily damaged by an Allied bombing raid. As a result, the Jumo 222 program was relocated to Oberursel near Frankfurt. These events caused major delays with all tests and engine work then in progress.
Various versions of the Jumo 222 were flown in approximately 11 aircraft: three Ju 52 test beds, six Ju 288s (V5, V6, V8, V9, V12, and V14), one Fw 191 (V6), and one He 219 (V16). Jumo 222 engines were also planned for the Heinkel He 219B and C and the Hütter Hü 211 heavy fighters. Engines were not ready for the He 219B and C airframes, and the two Hü 211 prototypes were destroyed while under construction during an Allied bombing raid in December 1944. Some sources state that Jumo 222 engines were fitted to a four-engine Heinkel He 177 (V101), as the burned out remains of this aircraft were found at Cheb in Czechoslovakia. However, examination of the aircraft reveals the engine’s exhaust stacks were in the standard four and eight o’clock positions for a Daimler-Benz DB 603 engine rather than the 2, 6, and 10 o’clock positions for the Jumo 222. The Jumo 222 was proposed for numerous other aircraft designs ranging from fighters, like the Focke-Wulf Ta 152, to bombers, like the Heinkel He 177. However, none of these plans came to fruition. A total of 289 Jumo 222 engines were built.
The Jumo 225 was conceived back in 1937 as a development of the basic Jumo 222. The Jumo 225 was a 36-cylinder engine with six banks of six cylinders. With the original 5.31 in (135 mm) bore and stroke, the Jumo 225 displaced 4,245 cu in (69.57 L). The engine was forecasted to produce 3,500–4,000 hp (2,610–2,983 kW) at 3,000 rpm and was 8 ft 10 in (2.69 m) long. The Jumo 225 was never built.
While the Jumo 222 was not trouble-free, its development progressed as well as could be hoped for considering it was a new engine design, the repeated changes to engine requirements and design, and that the ongoing war resulted in material shortages. Some contend that the changing Ju 288 and Jumo 222 requirements were intentionally made to cause the aircraft and engine to fail.

The 2,500 hp (1,864 kW) Jumo 222 E displayed at the Deutsches Museum in Munich. The two-stage supercharger added to the engine’s overall length. Note the revised induction system that incorporated aftercoolers and new intake manifolds. (Deutsches Museum image)
Heinrich Koppenberg was the managing director of Junkers, the only German company producing both aircraft and aircraft engines. Koppenberg had become a powerful man who worked himself into various positions that gave him control over many strategic resources. Erhard Milch was the Air Inspector General of the Luftwaffe and in charge of aircraft production. He had gained increasing control over aircraft procurement in Germany. Milch felt that Koppenberg and Junkers would have an aircraft production monopoly and economically ruin other companies if the current Ju 288, Jumo 222, and other company projects were successful. New large-scale Junkers production orders meant that resources at other companies would be allotted to produce Junkers products under license rather than develop their own. Some contend that Milch began to alter the official requirements just as they were about to be met by Junkers. After Ernst Udet, head of the T-Amt (Technisches Amt, Technical Office of the RLM), committed suicide on 17 November 1941, Milch took his place. Milch now had the power to dictate programs for the Luftwaffe. Acting as the RLM’s authority, Milch continued to change project requirements, which left Junkers to perpetually chase the goal. Koppenberg was imprisoned in April 1942 when Junkers repeatedly failed to achieve what the RLM asked of them. While the above may be true, it is also true that the Jumo 222 had its own design issues. Brandner felt the engine was “developed to death” with its numerous displacement changes and constant design revisions.
In Spring 1944, Japan and Germany entered negotiations for Japan to purchase production rights for the Jumo 222. An agreement was reached in September 1944 that included drawings, sample parts, and the assistance of Brandner in exchange for 10 million Reichsmarks. The trip was to be made via submarine, and the departure date was set for mid-January. However, Brandner was shifted to resolve issues with the Jumo 004 turbojet in December 1944 and never went to Japan. It is not clear if Jumo 222 parts and plans were ever sent.
Brandner was captured by the Soviets at the end of the war and was interned in the USSR until 1953. While there, he worked on the M-222 engine design, which was essentially a reconstruction of the Jumo 222. Although the Soviets had captured five examples of the Jumo 222, the M-222 engine was never built. Among other projects, Brandner led a team that developed the 12,000 hp (8,948 kW) Kuznetsov NK-12 turboprop engine that powered the Tupolev Tu-95 Bear and other aircraft.
In addition to the Soviets, the United States and the British captured a number of Jumo 222 engines at the end of the war. A Jumo 222 E was built up by the United States Army Air Force at Wright Field with the intent to test the engine’s performance. While the engine was mostly complete by the end of 1946, other priorities took precedence, and the captured Jumo 222 E was never tested. Most likely, this engine was returned to Germany in 1978. It is now on display at the Deutsches Museum in Munich and is the only Jumo 222 known to exist.
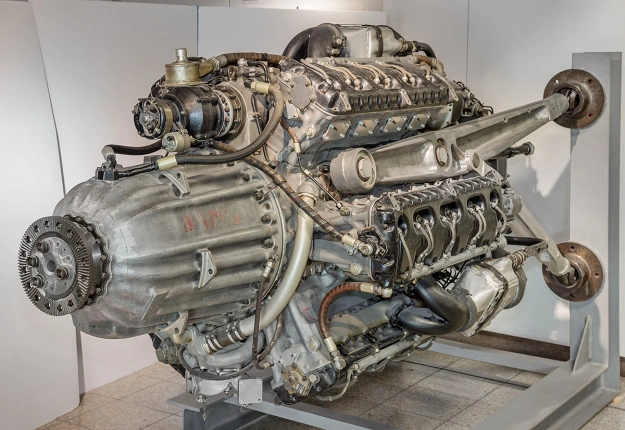
This Jumo 222 E was captured and sent to the United States for testing. It was most likely the engine that Wright Field planned to test in late 1946. The engine was returned to Germany in 1978. Note the starter mounted above the gear reduction housing. (Deutsches Museum image)
Sources:
– “The Junkers Jumo 222” by Kimble D. McCutcheon, Torque Meter Volume 6, Number 3 (Summer 2007)
– Junkers Flugtriebwerke by Reinhard Müller (2006)
– Flugmotoren und Strahltriebwerke by Kyrill von Gersdorff, et. al. (2007)
– Ein Leben Zwischen Fronten by Ferdinand Brandner (1973)
– Junkers Aircraft & Engines 1913–1945 by Antony Kay (2004)
– Jane’s All the World’s Aircraft 1945/46 by Leonard Bridgman (1946)
– Junkers Ju 288/388/488 by Karl-Heinz Regnat (2004)
– Heinkel He 219 by R. Francis Ferguson (2020)
– Dornier Do 217-317-417 An Operational Record by Manfred Griehl (1991)
– http://www.enginehistory.org/Piston/Junkers/Jumo222/Jumo222.shtml
– https://ww2aircraft.net/forum/threads/jumo-222-whats-the-truth.39301/
– https://digital.deutsches-museum.de/item/1978-17/